この記事は約19分2秒で読むことができます。

リーン生産方式:無駄を排除し、効率を最大化する究極のガイド
リーン生産方式は、無駄を排除し、効率を最大化することを目的とした経営戦略です。このアプローチは、もともとトヨタ自動車の生産システムから派生したもので、現在では製造業界を超えてさまざまな分野で採用されています。リーン生産方式の核心は、顧客に価値を提供する活動にのみ焦点を当て、それ以外の活動を「ムダ」と見なし、可能な限り排除することです。この方式では、品質の向上、コストの削減、納期の短縮が可能となり、結果として顧客満足度が向上します。
しかし、リーン生産方式を成功させるには、単に工程を改善するだけでは不十分です。組織文化の変革、従業員の積極的な参加、継続的な改善へのコミットメントが必要となるのです。このブログ記事では、リーン生産方式の基本原則、そのメリット、導入ステップ、そして実際にこの方式を取り入れた企業の事例を通じて、リーン生産方式がいかにビジネスの効率化と成長に貢献するかを解説します。
リーン生産方式は単なる製造技術ではなく、組織全体の思考方法と文化を変革する哲学であるとも言えます。この記事を通じて、リーン生産方式の基本的な概念を理解し、その実装がもたらす可能性について深く考え、皆さんのビジネスにおけるその適用を検討するきっかけになればと思います。無駄の削減と効率の向上は、競争が激しい今日のビジネス環境において、成功を左右する重要な要素です。その成功への鍵となるかもしれなりリーン生産方式について、一緒に学びましょう。
リーン生産方式の基本原則
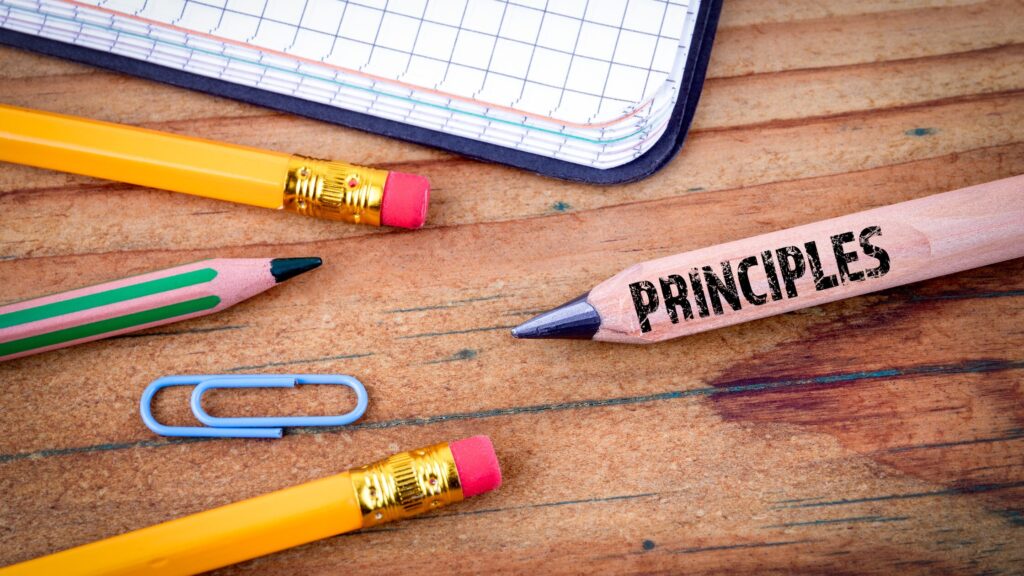
リーン生産方式は、顧客価値の最大化と無駄の排除を目指す経営哲学であり、これを実現するためには以下の5つの基本原則を守ることが重要です。これらの原則は、企業が効率的で柔軟な生産システムを構築し、競争力を高める上で不可欠と言えます。それでは、これらの原則が企業の運営にどのように貢献するかを見ていきましょう。
1. 価値の特定
リーン生産方式の最初の原則は、顧客が本当に価値を見出しているものを特定することです。価値の定義は顧客によって異なるため、企業は顧客のニーズや期待を深く理解する必要があります。価値を特定することで、企業はその価値を提供するために必要なプロセスに注力し、顧客にとって無価値な活動を排除することができます。
2. プロセスの可視化
価値を特定した後、企業はその価値を生み出す一連のプロセスを特定し、可視化する必要があります。このプロセスには、原材料の調達から製品が顧客に届くまでの全工程が含まれます。プロセスの可視化を行うことで、企業は無駄な手順や過剰な在庫、不必要な作業を明らかにし、それらを排除するための改善策を見つけることができます。れます。価値ストリームマッピングを通じて、企業は無駄なステップ、過剰な在庫、不要な作業を明らかにし、排除することができます。
3. フローの作成
無駄が排除されたら、次に、製品やサービスがスムーズに、かつ迅速に顧客に届けられるようにフローを作成します。フローの障害となる要因、例えば不均一な作業ロード、生産のボトルネック、不必要な工程の複雑さを取り除くことが目標です。これにより、生産時間の短縮、品質の向上、コストの削減が可能になります。
4. プル方式の導入
リーン生産方式では、実際の顧客需要に基づいて製品を生産するプル方式を推奨します。これは、在庫の過剰な蓄積を避け、生産と供給のプロセスをより効率的にするためです。プル方式では、次の工程は前の工程から必要な分だけ材料を「引っ張る」ため、過剰生産のリスクを最小限に抑えることができます。
5. 完璧を求めるプロセスの継続
リーン生産方式の最後の原則は、完璧を求めるプロセスの継続です。これは、企業が常にプロセスを見直し、改善の機会を探求し続けることを意味します。継続的な改善の文化を根付かせることで、企業は長期的な競争優位性を維持し、市場の変化に柔軟に対応することができます。
これらの原則に従うことで、企業は生産プロセスを最適化し、顧客に真の価値を提供する製品やサービスを生み出すことができます。リーン生産方式は、単にコストを削減するだけでなく、企業全体の効率性、柔軟性、品質を向上させるための戦略的アプローチとして機能します。
バリューチェーンとの違い
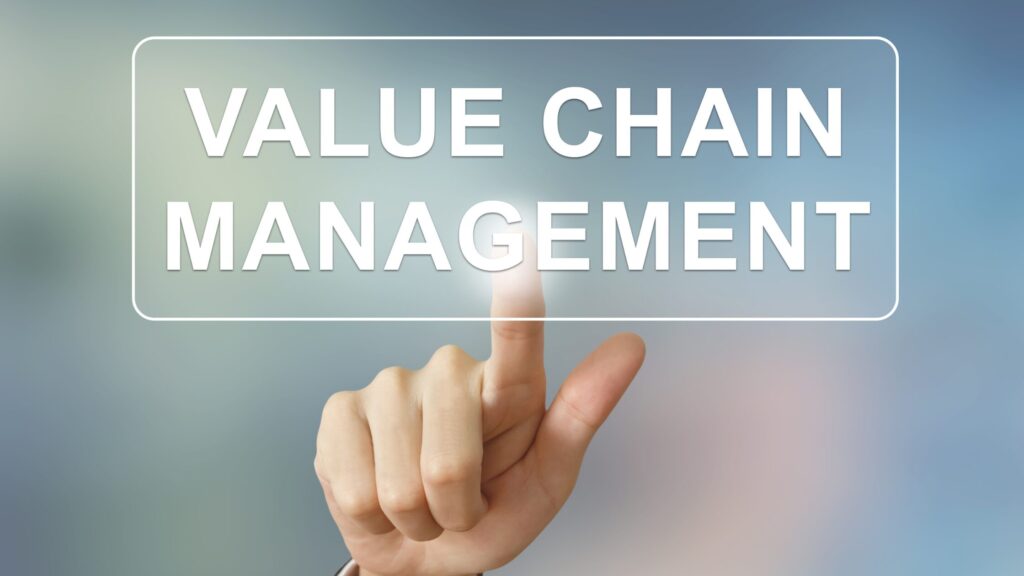
リーン生産方式とバリューチェーンは、どちらも組織が価値を創造し、競争優位性を確立する方法に焦点を当てていますが、アプローチと目的において異なります。
バリューチェーン
- 定義 : マイケル・ポーターによって導入された概念で、企業が製品やサービスを通じて顧客に価値を提供するために行う一連の活動を分析するフレームワークです。
- 目的 : 組織内の各活動が製品にどのように価値を加えているかを理解し、それぞれの活動で競争優位性をどのように確立できるかを特定することにあります。
- 構成要素 : バリューチェーンは、主要活動(製品の設計、製造、マーケティング、配送、アフターサービス)と支援活動(企業インフラ、人材管理、技術開発、調達)に分かれています。
- 焦点 : 競争優位性を確立するために、組織内の特定の活動をどのように管理し、最適化するかに焦点を当てます。
バリューチェーンの記事はこちら
-
バリューチェーンの基本 : あなたのビジネスを変革する戦略
この記事は約12分8秒で読むことができます。 目次 / Contents バリューチェーンの基本 : あなたのビジネスを変革する戦略バリューチェーンとは何か主要活動と支援活動の詳細バリューチェーンの活 …
続きを見る
リーン生産方式
- 定義 : トヨタ生産システムから発展した概念で、無駄を排除し、プロセスの効率を最大化することを目指す経営戦略です。
- 目的 : 製品やサービスの生産プロセス全体を通じて無駄を排除し、顧客にとっての価値を最大限にしながらコストを削減することにあります。
- 構成要素 : リーン生産方式は、価値の特定、プロセスの可視化、フローの作成、プル方式の導入、継続的な改善などの原則に基づいています。
- 焦点 : 生産プロセス全体を通じて無駄を特定し、排除することにより、全体的な効率と柔軟性を向上させることに焦点を当てます。
主な違い
- アプローチの焦点 : バリューチェーンは組織内の個々の活動がどのように全体の価値を高めるかに焦点を当てていますが、リーン生産方式は生産プロセス全体の効率化と無駄の排除に焦点を当てています。
- 目的 : バリューチェーンは競争優位性の確立に重点を置いていますが、リーン生産方式は顧客価値の最大化とコストの削減を主な目的としています。
これら二つの概念は、ビジネスの運営と管理において相互補完的な役割を果たすことができます。バリューチェーン分析を通じて企業が競争優位性を理解し、リーン生産方式を適用することで、その優位性を実現し、さらに強化することが可能です。
リーンスタートアップとは?
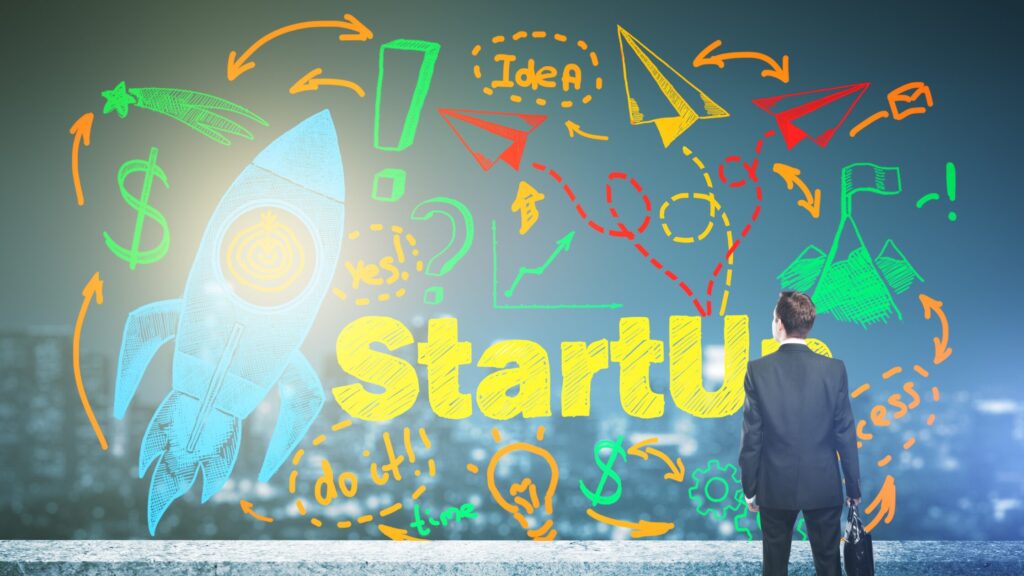
リーンスタートアップは、エリック・リースによって提唱されたスタートアップ企業のための方法論で、製品開発の無駄を省き、スタートアップの成功率を高めることを目的としています。このアプローチは、従来の製品開発モデルが持つ時間と資源の浪費を最小限に抑え、迅速な市場検証を通じて顧客のニーズに合った製品を開発することに焦点を当てています。
リーンスタートアップの主な原則
- ビルド・メジャー・ラーンのループ : 製品開発のプロセスを「ビルド(構築)→メジャー(測定)→ラーン(学習)」の繰り返しとして捉え、迅速なフィードバックループを通じて製品を改善していきます。最小限の労力で製品のプロトタイプ(最小実行可能製品、MVP)を作成し、市場の反応を測定、そのデータから学び、製品を迅速に改善していきます。
- 最小実行可能製品(MVP = Mimimun Viable Product): MVPは、製品のコア機能に限定したバージョンで、最小限の労力で市場に投入されます。これにより、大規模な投資を行う前に顧客の反応をテストし、製品の方向性を早期に検証することができます。
- バリデーションされた学習 : スタートアップは、市場と顧客から得られる具体的なデータを基に学習を進め、ビジネスモデルや製品の仮説を検証します。このプロセスを通じて、製品の方向性や機能の追加・修正が行われます。
- ピボットまたは継続 : 市場の反応やバリデーションされた学習を基に、スタートアップは製品や戦略の大幅な変更(ピボット)を行うか、現在の計画を継続する(粘り強さ)かを決定します。この判断は、スタートアップが長期的な成功を収める上で重要です。
リーンスタートアップは、不確実性が高い市場環境での製品開発に対して、リスクを低減し、より柔軟に対応するための方法論です。顧客との継続的な対話と学習を通じて、顧客が本当に求める価値を提供する製品を開発することを目指しています。このアプローチは、スタートアップだけでなく、大企業の新規事業や製品開発においても応用されるようになっています。
リーンスタートアップはリーン生産方式の応用なのか?
リーンスタートアップは、リーン生産方式からインスピレーションを受けた方法論ですが、それを直接的な応用というよりは、リーンの原則を新たな文脈であるスタートアップ企業の製品開発とビジネスモデルの検証に適用したものです。リーン生産方式が製造業での無駄の排除と効率化に焦点を当てるのに対し、リーンスタートアップは不確実性が高い市場での事業機会を探求するスタートアップ企業において、リスクを管理し、迅速な学習と製品開発のプロセスを通じて、顧客に真の価値を提供する方法を模索します。
リーン生産方式とリーンスタートアップの共通点
- 無駄の排除 : 両方のアプローチは、不必要な工程や活動を排除し、効率を最大化することを目指します。
- 価値の創造 : 顧客が価値を見出す製品やサービスの提供に焦点を当てます。
- 継続的な改善 : カイゼン(改善)の概念を通じて、継続的な学習と進化を重視します。
主な違い:
- 適用範囲 : リーン生産方式は主に製造業における生産プロセスの最適化に関連していますが、リーンスタートアップは製品やサービスが市場に受け入れられるかどうかを検証する新しいビジネスイニシアチブに適用されます。
- 目的 : リーン生産方式は効率的な生産とコスト削減に主眼を置きますが、リーンスタートアップは市場の不確実性の中で迅速に学習し、製品を市場に合わせて進化させることに重点を置いています。
- アプローチ : リーン生産方式は既存のプロセスの改善に焦点を当てていますが、リーンスタートアップはビジネスモデルの検証と製品の市場適合性を確認するための仮説駆動型のアプローチを採用しています。
リーンスタートアップは、リーン生産方式の基本原則をビジネスモデルの開発と製品イノベーションの文脈に適応させたものであり、スタートアップのリスクと不確実性を管理するための強力なフレームワークと言えるでしょう。
リーン生産方式のメリット
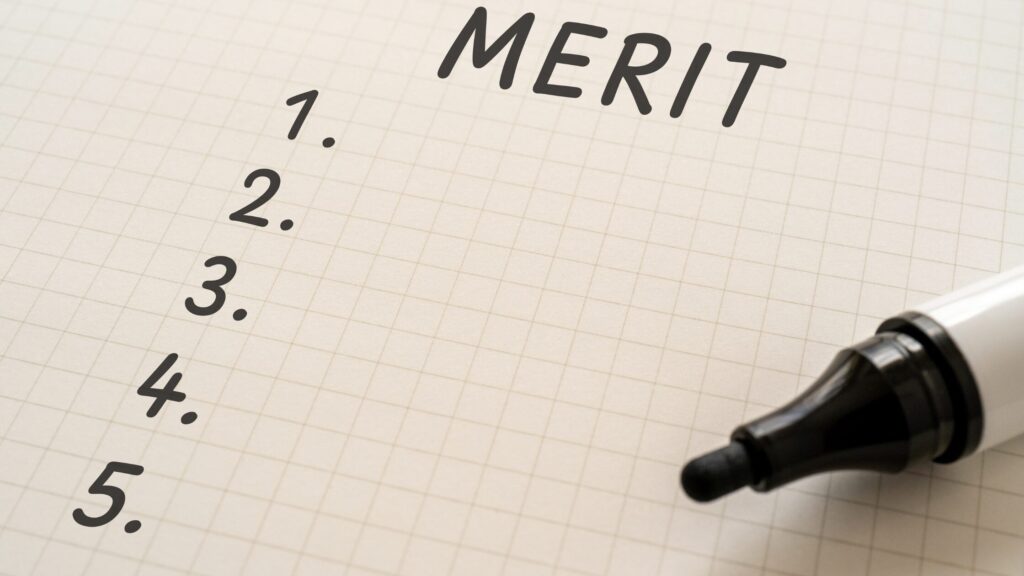
リーン生産方式は、無駄を排除し、プロセスの効率を最大化することを目的とする経営戦略です。このアプローチには多くのメリットがあり、製造業をはじめとする様々な業界で採用されています。ここでは、リーン生産方式の主なメリットについて詳しく見ていきましょう。
効率の向上
リーン生産方式の核心は、プロセスから無駄を排除することにあります。無駄とは、価値を加えないあらゆる活動のことで、例えば過剰な在庫、不必要な移動、過剰な加工などが含まれます。これらの無駄を排除することで、プロセスの効率が向上し、生産性が高まります。結果として、同じ時間とリソースでより多くの製品を生産できるようになり、企業の競争力が強化されるのです。
コスト削減
効率の向上は、直接的にコスト削減につながります。無駄なプロセスを排除することで、不要な材料の消費やエネルギーの使用を減らし、製造コストを削減することができます。また、過剰な在庫が減少すると、在庫管理にかかるコストや廃棄リスクも低下します。これらのコスト削減は、企業の利益率を向上させる重要な要素です。
品質の向上
リーン生産方式では、品質の向上も重要な目標の一つです。無駄の排除とプロセスの最適化により、製品の製造過程が一貫性を持ち、エラーが減少します。また、従業員が品質向上により集中できる環境が整うことで、製品の品質がさらに向上します。高品質な製品は顧客満足度を高め、リピート購入やブランドの信頼性向上につながります。
納期の短縮
プロセスの効率化と無駄の排除は、製品の生産から配送までの時間を短縮します。これにより、市場への製品の投入速度が速くなり、顧客の要求に迅速に応えることが可能になります。納期の短縮は、顧客満足度の向上とともに、変化する市場のニーズに柔軟に対応する企業の能力を示す指標となります。
従業員の参加とモチベーション
リーン生産方式は従業員の積極的な参加を奨励します。プロセス改善のためのアイデアが従業員から生まれることを促し、改善活動における彼らの役割を重視するのです。このような参加型の文化は、従業員のモチベーションを高め、職場の士気を向上させます。従業員が自らの仕事に責任を持ち、改善に貢献することで、全体としての組織の効率性と生産性が向上します。
持続可能性の向上
最後に、リーン生産方式は持続可能性の観点からもメリットがあります。無駄の排除と効率の向上は、資源の使用量を減らし、廃棄物の削減に貢献します。これにより、企業の環境負荷が軽減され、持続可能な生産活動へと繋がります。
リーン生産方式には、これらのように多岐にわたるメリットがあります。これらのメリットは、企業がより効率的で、コスト削減効果が高く、顧客に対してより高い価値を提供できる製品を生み出すことを可能にします。また、組織全体の持続可能性と競争力を高めることにも貢献します。
リーン生産方式の実装ステップ
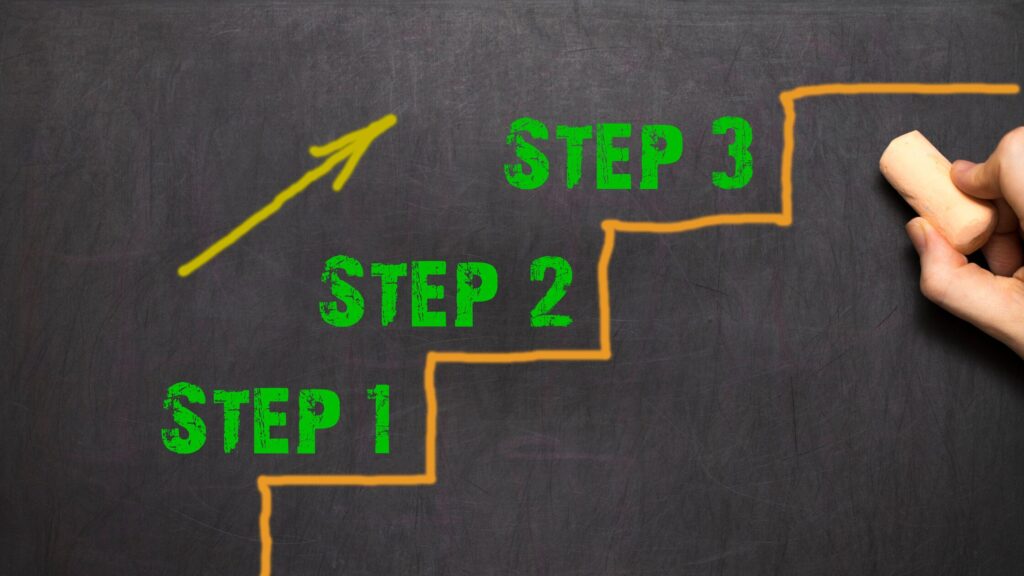
リーン生産方式の実装は、組織における深い変化をもたらすプロセスです。この変化を成功させるためには、計画的かつ段階的なアプローチが必要です。以下は、リーン生産方式を実装するためのステップを説明します。
1. コミットメントの確保
リーン生産方式の実装はトップダウンのアプローチが必要であり、経営層の完全なコミットメントから始めます。経営陣は、リーン変革のビジョンを明確にし、組織全体にその重要性を伝える責任があります。経営陣のサポートは、プロジェクトに資源を割り当て、従業員の参加を促すために不可欠です。
2. リーン文化の構築
リーン生産方式は、単なるツールや技術の導入以上のものであり、組織文化の変革を伴います。リーン文化を構築するには、従業員全員が継続的な改善の価値を理解し、それに貢献することが求められます。教育とトレーニングを通じて、リーンの原則と価値を組織内に浸透させます。
3. チームの形成
専門のリーン実装チームを形成し、プロジェクトの指導と実行を任せます。このチームは、リーンの専門知識を持ち、組織内の様々な部門から選ばれたメンバーで構成されるべきです。チームは、リーンの実装計画を立案し、各部門と協力しながらプロジェクトを進めます。
4. 現状分析と価値ストリームマッピング
組織の現状を評価し、プロセスの価値ストリームマッピングを行います。このステップでは、価値を生み出す活動と無駄な活動を識別し、プロセス全体の可視化を通じて改善の機会を見つけ出します。
5. 最小実行可能プロセスの実装
改善の機会を特定したら、小規模な実験を通じてそれらの改善を試みます。最小実行可能プロセス(MVP)の概念を適用し、小さなスケールでプロセスの改善を行い、その結果を評価します。成功した改善は組織全体に展開されます。
6. 継続的な改善
リーン生産方式の実装は、一度で完了するものではありません。プロセスの改善、評価、調整を継続的に行い、組織全体でのカイゼン(改善)の文化を育てます。従業員からのフィードバックを積極的に取り入れ、改善のアイデアを常に探求します。このプロセスは、組織が進化し続け、市場の変化に柔軟に対応できるようにするために重要です。
7. 成果の測定とフィードバック
リーン実装の効果を測定するために、具体的な指標を設定し、定期的に成果を評価します。生産性、品質、顧客満足度、納期の短縮など、改善の影響を示す指標を用いて、プロジェクトの進捗をモニタリングします。測定結果を基に、プロセスのさらなる改善や調整を行い、必要に応じて新たな目標を設定します。
8. 成功事例の共有
リーン実装における成功事例や学んだ教訓は、組織内で積極的に共有します。成功事例を共有することで、他の部門やチームにもポジティブな影響を与え、リーン文化の浸透を促進します。また、従業員のモチベーションを高め、組織全体の改善意欲を刺激します。
9. 柔軟な対応とピボット
リーン生産方式の実装中には、予期せぬ障害や新たな課題が発生することもあります。そのため、プランに固執するのではなく、状況に応じて柔軟に対応し、必要に応じて戦略を調整(ピボット)することが重要です。継続的な学習と適応を通じて、リーン実装の戦略を最適化します。
10. 組織全体への展開
初期の成功を基に、リーン生産方式を組織全体に展開します。全社的な取り組みとして、リーンの原則と実践を組織のあらゆるレベルに適用し、全従業員がリーン文化の一部となるよう努めます。
リーン生産方式の実装は、組織にとって大きな変革を意味しますが、正しく実施すれば、効率性の向上、コスト削減、品質の向上、顧客満足度の向上など、数多くのメリットを享受できます。リーン実装のプロセスは継続的な改善が要求され、組織が常に進化し続けるための手段とも言えます。
リーン生産方式の課題と解決策
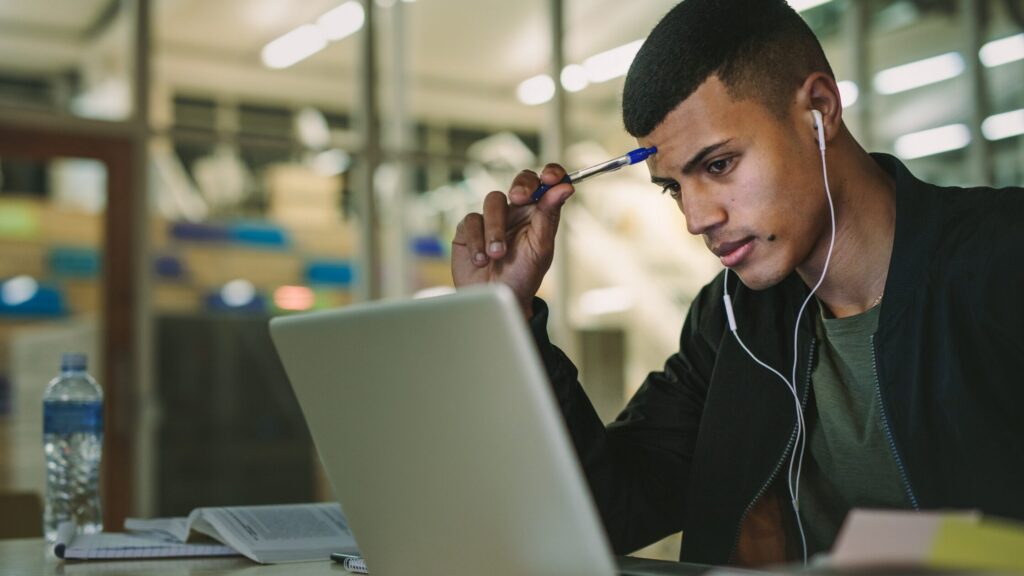
リーン生産方式の実装は、多くの企業にとって顕著な成果をもたらす一方で、様々な課題に直面することもあります。ここでは、これらの課題とそれらに対する解決策を探ります。
1. 文化的抵抗
課題 : 組織文化の変更に対する抵抗は、リーン生産方式の実装において最も一般的な課題の一つです。従業員や管理層が新しい方法論や変更に抵抗することがあり、これがプロジェクトの進行を妨げる可能性があります。
解決策 : この問題に対処するためには、経営層が変革の重要性を明確に伝え、全員がビジョンを共有することが重要です。また、従業員を変革プロセスに積極的に関与させ、フィードバックを求めることで、彼らの参加を促します。
2. 継続的な改善の維持
課題 : 初期の成功後に継続的な改善活動を維持することは困難を伴います。従業員のモチベーションの低下や焦点の不明瞭さが原因で、リーンの取り組みが徐々に衰退することがあります。
解決策 : 継続的な改善を促進するためには、小さな成功を祝う文化を育むとともに、改善活動を日常業務の一部として組み込むことが効果的です。また、リーンの取り組みを組織のパフォーマンス指標に統合し、目に見える成果を通じてモチベーションを維持します。
3. 適切な知識とスキルの欠如
課題 : リーン生産方式を効果的に実装するには、適切な知識とスキルが必要です。従業員や管理層がリーンの原則やツールに不慣れな場合、実装プロセスが遅れる可能性があります。
解決策 : 教育とトレーニングは、この課題に対する鍵です。従業員と管理層にリーンの原則、ツール、およびベストプラクティスに関する包括的なトレーニングを提供し、定期的に知識の更新を行います。
4. プロセスの標準化と柔軟性のバランス
課題 : プロセスの標準化はリーン生産方式の重要な要素ですが、過度の標準化は柔軟性を損なう可能性があります。市場や顧客のニーズが変化すると、企業は迅速に対応する必要があります。
解決策 : 効果的なリーン実装は、標準化されたプロセスと柔軟性の適切なバランスを見つけることにあります。これは、定期的なレビューとプロセスの調整を通じて達成できます。また、従業員が変更を提案しやすい環境を作ることが重要です。
5. サプライチェーンとの調整
課題 : リーン生産方式は、サプライチェーン全体での協力を必要とします。サプライヤーや配送業者がリーンの原則に従わない場合、効率的なプロセスが妨げられる可能性があります。
解決策 : サプライチェーン内のパートナーと密接に協力し、リーンの原則を共有します。サプライヤーに対するトレーニングプログラムを提供することで、サプライチェーン全体の効率性を向上させることができます。
リーン生産方式の実装は、これらの課題に直面する可能性がありますが、適切な戦略とコミットメントをもってこれらに対処することで、持続可能な改善と組織の成長を実現することができます。
事例研究
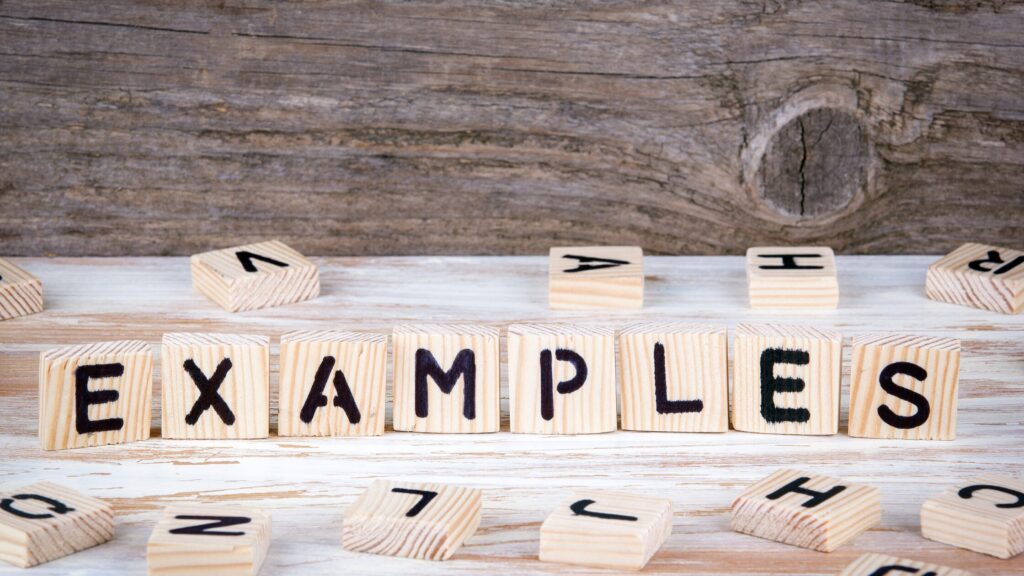
リーン生産方式の効果を示す事例研究として、トヨタ自動車のトヨタ生産方式(TPS : Toyota Production System)の成功は広く知られています。しかし、リーン生産方式は製造業界にとどまらず、様々な業界で効果を発揮しています。ここでは、異なる業界でのリーン生産方式の成功事例を探ります。
事例1 : ヘルスケア業界 – バージニア・メイソン医療センター
バージニア・メイソン医療センターは、リーン生産方式を医療業界に導入した先駆者の一つです。彼らは「バージニア・メイソン生産方式(VMP : Virginia Mason Production System)」と呼ばれるシステムを開発し、患者ケアの質の向上、プロセスの効率化、コスト削減を実現しました。具体的には、患者の待ち時間の削減、治療プロセスの改善、不要な医療行為の排除に成功しました。この取り組みにより、患者満足度が向上し、医療コストの削減にも繋がりました。
事例2 : 製造業界 – ジョン・ディア
農業機械メーカーであるジョン・ディアは、リーン生産方式を採用して生産性を大幅に向上させました。彼らは生産ラインの再設計、在庫レベルの最適化、品質管理プロセスの改善を行いました。これにより、製造リードタイムが短縮され、品質が向上し、顧客への納品時間が短くなりました。ジョン・ディアの取り組みは、製造業におけるリーン生産方式の成功例として広く認識されています。
事例3 : 小売業界 – スターバックス
スターバックスは、カフェ業界においてリーン生産方式を取り入れたことで知られています。彼らは、顧客の待ち時間を減らし、店舗運営の効率を向上させるために、店舗内のオペレーションを再設計しました。具体的には、コーヒー製造プロセスの改善、作業ステーションの最適化、エラーの削減に取り組みました。これらの改善により、顧客サービスのスピードと品質が向上し、顧客満足度が高まりました。
事例4: IT業界 – デル
デルは、カスタマイズされたPCの製造と直販モデルで知られるIT企業です。リーン生産方式の原則を採用することで、デルは注文から配送までの時間を大幅に短縮しました。具体的には、サプライチェーンの効率化、在庫コストの削減、顧客ニーズに迅速に対応する生産システムの構築に成功しました。デルの事例は、リーン生産方式がいかに顧客中心のビジネスモデルに貢献できるかを示しています。
これらの事例は、リーン生産方式が製造業だけでなく、ヘルスケア、小売、ITなど様々な業界で効果を発揮できることを示しています。リーン生産方式を成功させるためには、組織全体のコミットメント、文化の変革、継続的な改善への取り組みが不可欠です。これらの事例から学ぶことで、他の企業もリーン生産方式の実装において成功を収めることができるでしょう。
まとめ
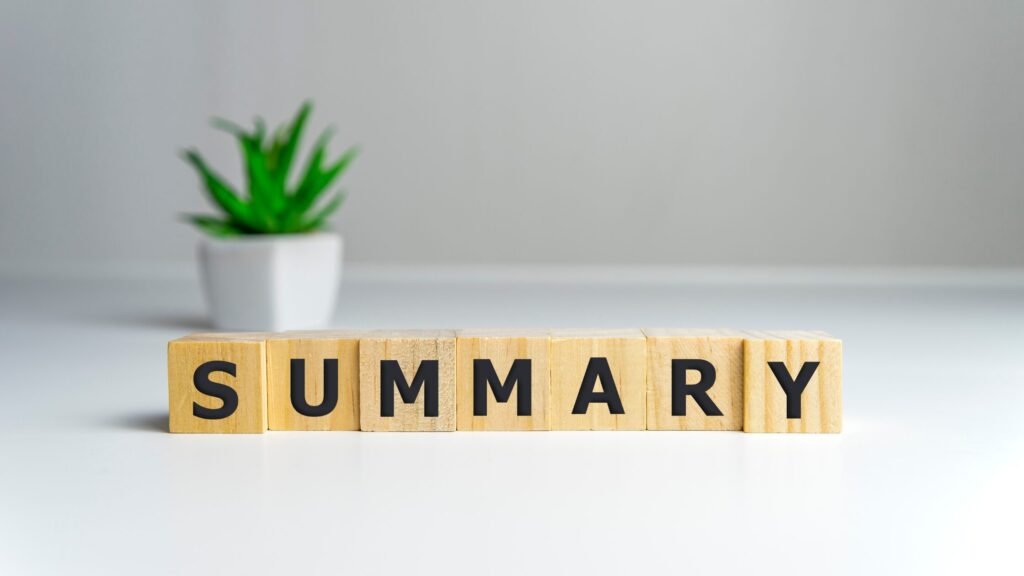
リーン生産方式は、無駄を排除し、効率を最大化することを目的とした経営戦略です。このアプローチは、トヨタ自動車によって開発されたトヨタ生産方式から広がり、今日では製造業界を超えて多岐にわたる分野で採用されています。リーン生産方式の実装は、企業にとって多くのメリットをもたらします。これには、効率の向上、コスト削減、品質の向上、納期の短縮、従業員のモチベーション向上、そして持続可能性の向上が含まれます。しかし、その実装過程では、文化的抵抗、継続的な改善の維持、適切な知識とスキルの欠如などの課題に直面することもあります。
これらの課題にもかかわらず、リーン生産方式を成功裏に実装した企業の事例研究は、その効果を明確に示しています。ヘルスケアから製造業、小売、IT業界に至るまで、リーンの原則は幅広い業界で価値を創造し、業務の効率化と顧客満足度の向上を実現しています。これらの成功事例は、適切な戦略と組織全体のコミットメントがあれば、どのような業界でもリーン生産方式を効果的に実装できることを示しています。
リーン生産方式は単なる生産効率化の手法ではなく、組織全体の文化の変革を促す強力なフレームワークとも捉えることができるものです。継続的な改善の実行及び従業員の積極的な参加を促し、顧客価値の最大化を目指すこのアプローチは、今後も多くの企業にとって価値ある戦略となるでしょう。
個別無料説明会(オンライン)について
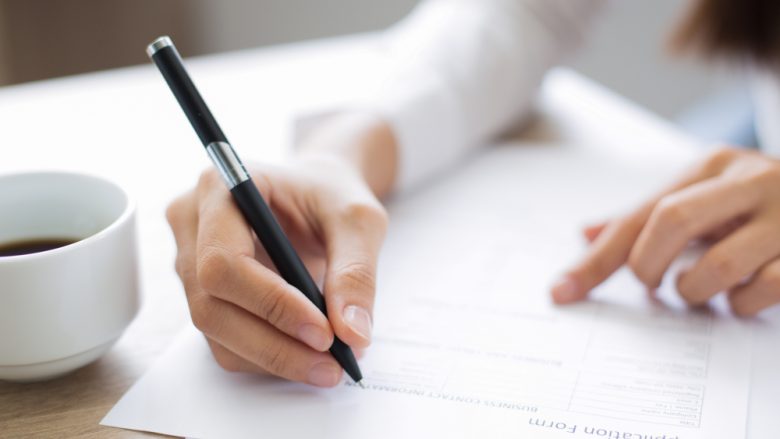
ライフコーチングを受けたい方はオンライン無料説明会へお申し込みください。
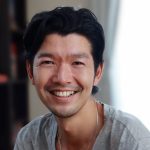
説明会は代表の刈谷(@Yosuke_Kariya)が担当します!お待ちしています!
コーチング有料体験について
実際にコーチングを体験してみたい方向けに、有料のコーチング体験も用意しております。ご興味のある方は以下をクリックください。
-
コーチング体験(有料)| ライフコーチング |【東京・コーチ歴13年・実績3000時間】
この記事は約4分3秒で読むことができます。 目次 / Contents コーチング体験(有料)のお申し込みページへようこそ!対象クライアント様代表コーチ刈谷洋介のご紹介体験セッションの流れコーチング有 …